Why should you shift from Industry 3.0 to 4.0?
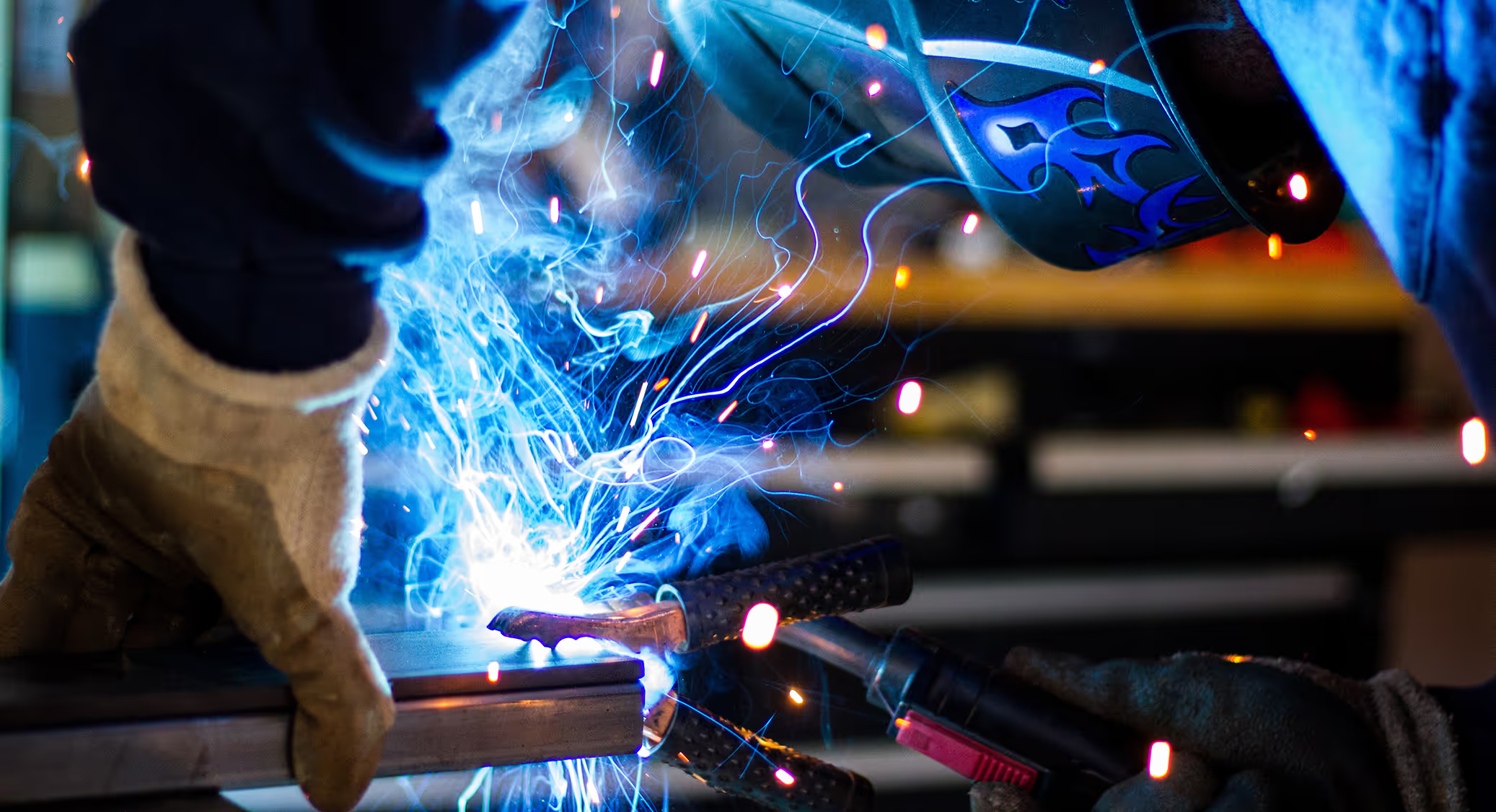
Often you only notice that a phase of an evolution is over when the next one arrives. History doesn’t run in clearly defined periods - after a while you just notice that there are suddenly a lot of new changes. The same is happening in the history of the manufacturing industry, where new innovations are always the catalyst of upheavals. By now, we can distinguish four different periods:
Industry 1.0
In the 1800s, water- and steam-powered machines were developed. The use of these metallic machines led to the first industrial revolution and the start of mass production. We saw a shift from ‘businesses’ to ‘industries’. It might seem like a trivial step, but the consequences were major and defined our way of working for centuries up and until today.
At the time the machines were extremely rudimentary, but they were very powerful and tireless. They had some disadvantages too: the machines were high in maintenance, had an inefficient energy consumption and their processing speeds were limited.
Industry 2.0
A century later, electricity became the primary source of power. It preludes the invention of the telegraph which, combined with the railroad, spearheaded the rapid transport of people and ideas. Industry 2.0 marks the beginning of mass production, which was particularly important in the automobile industry.
Industry 3.0
The last decades of the 20th century was marked by the invention of transistors, chips and processors which led to the development of the computer as we know it today. Thanks to the development of the internet, ideas and data could be exchanged rapidly. Automation became the norm in fabric halls, where PLC software conquered the place.
This is where most companies are today. There’s an even more rapid exchange of ideas and data than before, while data logging became possible too. Now, more and more people start to realize we should do something with the data.
Industry 4.0
Enter Industry 4.0, the era which focuses on data gathering. Thanks to the Internet of Things, machines are provided with sensors that send data to the cloud. AI and cloud computing can digest the raw data and feed it back as easy-to-understand input, which leads to complex and auto-adjustable machines that are still easy to handle.
Despite the huge potential of these innovations, few companies already made the shift to Industry 4.0. Why should you care? In his webinar, Machine Learning Engineer Ward will give an overview of the benefits, but here’s already a sneak preview:
- More and more large customers require smart machines.
- Large machine manufacturers such as Beckhoff or Siemens are already rolling out their first smart devices.
- Smart machines will become the standard and the challenges require large efforts that will not come instantaneously. It is better to go ahead or keep the same pace as the rest of the manufacturers.
If you’d like to know more or ask questions to one of our experts, join us this Thursday for Ward’s webinar!