How we helped Melexis modernise their internal semiconductor testing infrastructure
Melexis, a global microelectronics supplier specialising in automotive solutions and beyond, relies on rigorous testing to guarantee the quality of the millions of chips they produce daily. Working in blended teams, we optimised the software that runs the test programs, further improving its reliability and empowering Melexis’ engineers to create and execute test programs more efficiently. This strategic collaboration has modernised their critical testing infrastructure, providing a significant advantage.
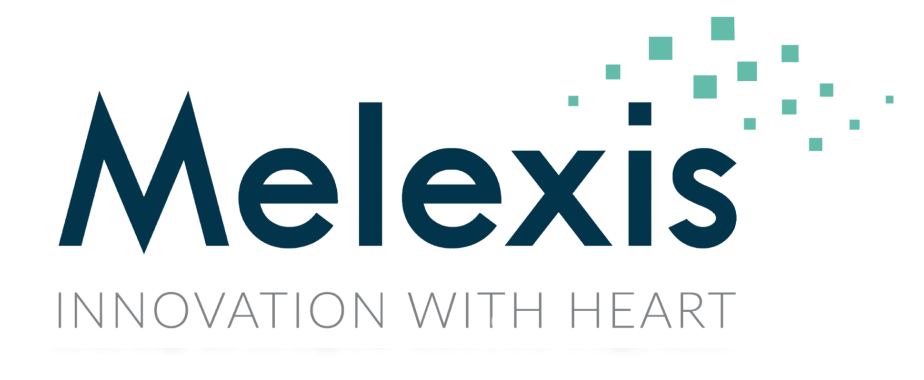
Modernising global testing infrastructure to maintain quality standards across multiple sites whilst managing complex test programmes.
Providing the right teams and experts to improve infrastructure, optimise product, and develop a long-term strategic planning.
Prioritising the most valuable elements, we adopted a product-centric approach, ensuring the internal tool was customised to meet the needs of Melexis’ employees and engineers.
Boosting efficiency and utilisation whilst giving Melexis a competitive edge through superior dynamic testing capabilities.
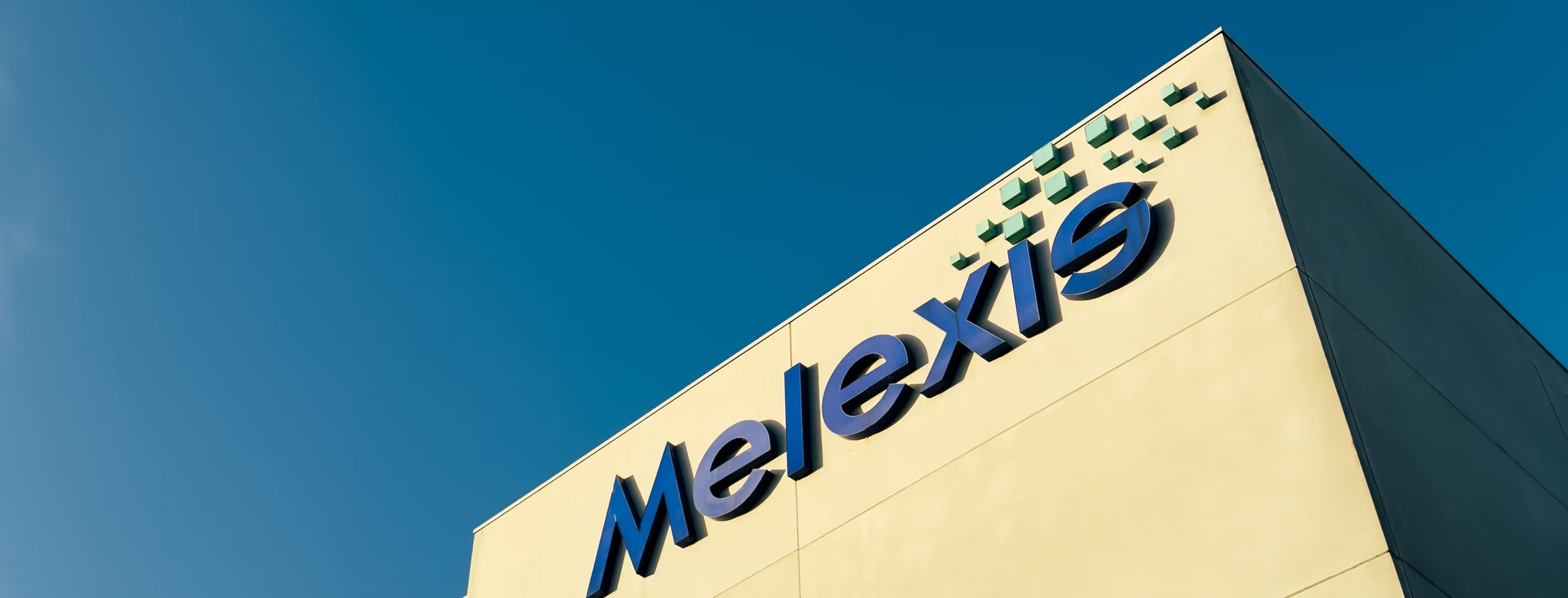
01 — CHALLENGE
Scaling quality in zero-failure environment
Melexis, a global semiconductor company, is headquartered in Belgium and employs over 2,000 people in 20 locations worldwide. They excel in creating high quality chip solutions for a broad range of applications (mainly within the automotive industry). Operating under strict IATF standards, Melexis must ensure every single chip meets rigorous quality requirements before reaching automotive customers. Testing isn't just a quality check at Melexis—it's a critical business function.
Melexis operates across five global manufacturing sites and 10-12 development centres, managing test programs for multiple product families that require frequent configuration updates. This complex operation demanded a robust, efficient, and standardised testing infrastructure. "We have to test every single chip, every single component going to the customer has to fulfill those strict requirements," shares Geert Casteleyn, Program Manager Smart Factories at Melexis.
The collaboration focused on enhancing their internal testing tool, essential for testing every single chip according to strict automotive industry standards. The existing software, while functional at an engineering level, needed significant improvements to scale across their global operations and support more efficient testing processes.
02 — SOLUTION
Modernising testing infrastructure
After initial internal development efforts, Melexis recognised the need for external expertise to scale their solution effectively-and chose In The Pocket as their collaborator. "What sets In The Pocket apart is their genuine commitment to our success. It’s not about just fulfilling a contract - they’re actively looking for ways to add value because they see our success as their success," says Piet De Ceuleners, Global IT Director at Melexis.
To start with, we improved the build process, while keeping the inputs and outputs the same, so the result could replace the current process without any changes. In order to have an overview of what is happening behind the screens, we developed a web platform. The platform displays the hierarchical structure of these test programs and their availability across different manufacturing centres. Users can easily view not only which test programs are available but also examine how their inner Docker layers are constructed.
Previously, understanding a test program's construction required navigating through multiple services like GitLab pipelines, Artifactory UI, ERP, and TPP, with no single source providing complete information. Our web platform now consolidates all essential data, showing both availability (across sites and production readiness) and traceability (Docker layers and program-specific tooling). This consolidation not only saves time in information gathering but also enables easier comparison between test programs, with the recent addition of production readiness management capabilities. Several parameters can be reviewed, such as availability and reliability so errors in the underlying process can be solved faster.
Finally, we improved and stabilise their desktop software client which runs at the heart of their shopfloor. While the platform offers many capabilities, its key value lies in allowing different test program configurations to run automatically, significantly improving runtime and testing efficiency. We also created a roadmap to keep adding new features where and when necessary.
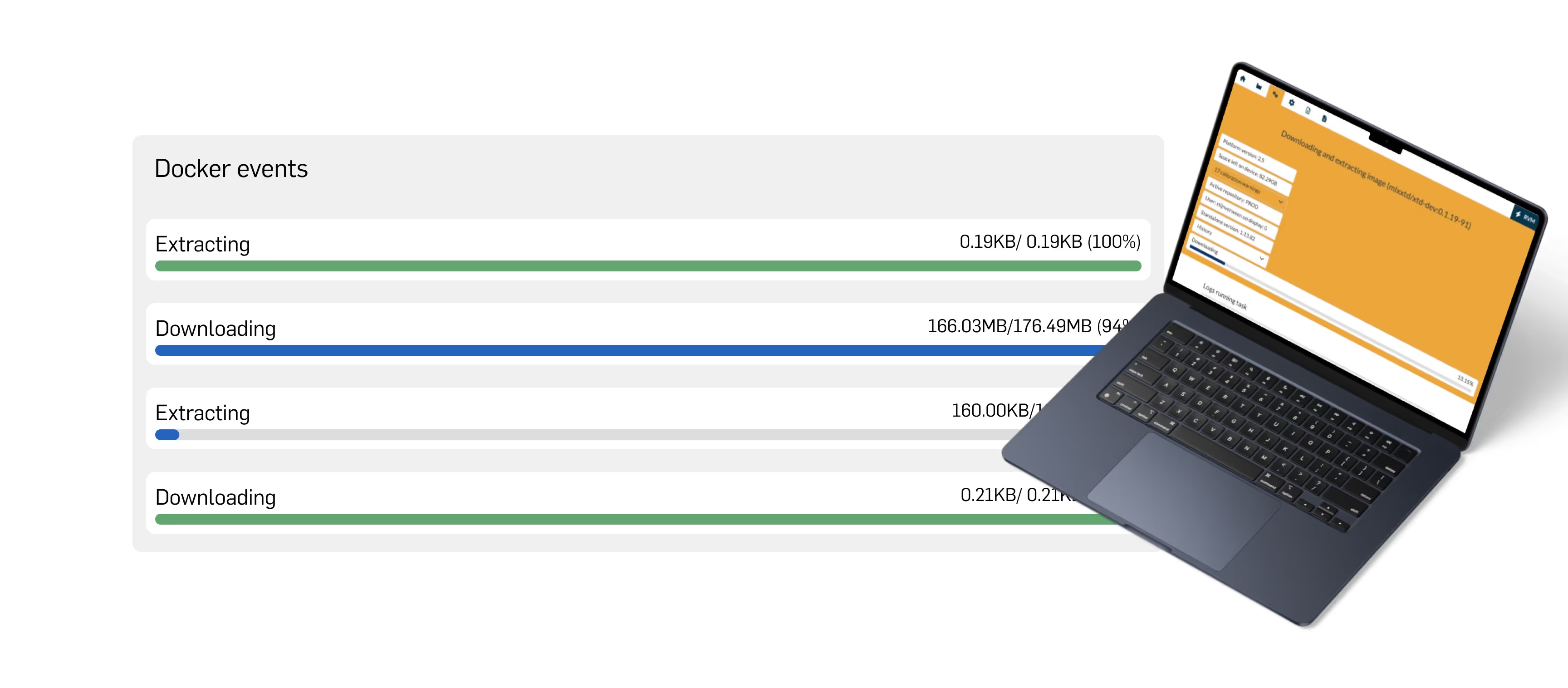
03 — APPROACH
Product thinking in action
“The product team concept is key for us. We wanted a collaborator who thinks with us on how to improve our solutions and processes,” says Piet. The transformation began with a strategic product mindset focused on delivering measurable outcomes. Through extensive user interviews and research, we identified critical pain points in the existing system. This discovery phase led to the creation of a solution opportunity tree, carefully linking specific features to challenges and desired outcomes. With this understanding, we developed a user-centric roadmap that prioritised the most valuable improvements.
Working with a complex codebase that had evolved over more than 10 years required careful consideration and planning. We used event storming sessions to map out processes and uncover additional improvement opportunities. This helped us navigate the intricate landscape of chip testing and manufacturing while maintaining system stability throughout the transformation.
The second phase brought significant enhancements to the system, as we introduced observability layers and monitoring capabilities, ensuring better visibility into system performance. During the collaboration, we also made a significant impact on their validation methodology by introducing our product-release-cycle approach.
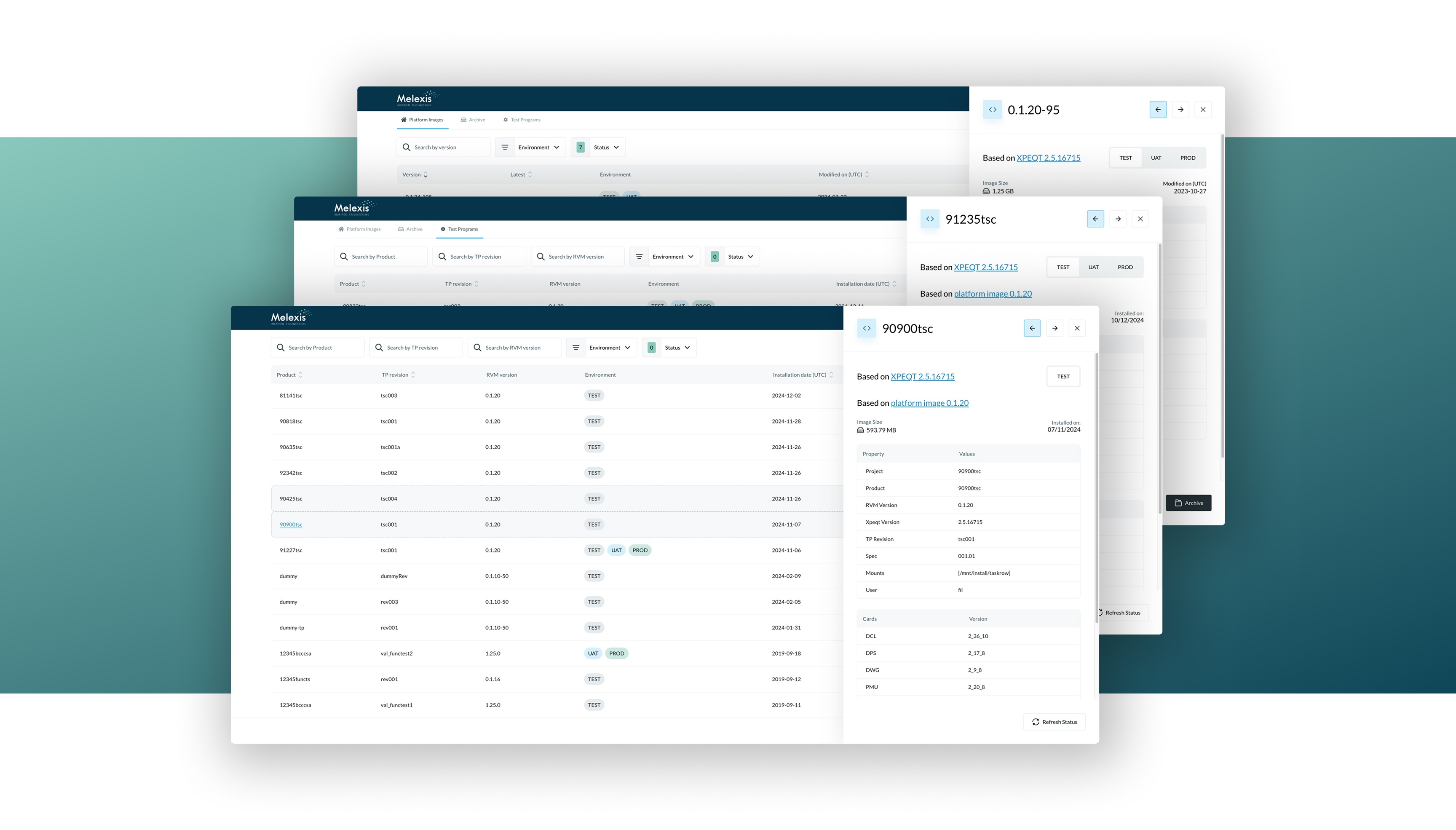
04 — OUTCOME
Ongoing collaboration and future plans
The new, robust testing infrastructure not only meets today's demanding requirements but also positions Melexis for future growth and innovation in the semiconductor industry. "The dynamic testing capabilities we've developed with ITP have given us a significant competitive advantage. What we're doing now is beyond industry standards - no one else can convert testing machines this dynamically in production," reveals Geert.
We made the life of test engineers and operators easier and the processes they use more efficiently, as they can run several versions of the tester's operating system more easily without the need of completely reconfiguring the tester each time. This results in a maximised utilisation of their testing facilities, which in its turn results in a faster time to market. "For every minute in our test cycle that requires operator intervention, we need to add one full-time operator to handle testing across all our production batches," concludes Geert.
The collaboration continues to evolve, with future plans focused on streamlining driver changes, enhancing observability, and optimising end-to-end processes across the testing ecosystem.